Accelerating Virtual Factories: NVIDIA's Breakthrough in AI-Powered Simulations
Accelerating Virtual Factories: Discover NVIDIA's revolutionary AI-powered simulations that enable reliable, cost-effective robotic automation. Explore the cutting-edge research enabling real-time virtual factories with unparalleled precision and speed.
February 17, 2025
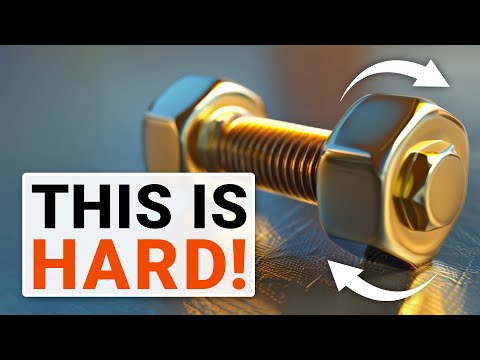
Discover how NVIDIA's groundbreaking AI technology is revolutionizing virtual worlds, enabling simulations that are 10,000x faster than ever before. Explore the incredible advancements in robotic assembly, collision detection, and real-time performance that are paving the way for a new era of virtual factories and automated manufacturing.
Exploring the Challenges of Robot Arms: From Expensive Customization to Unreliable General-Purpose Solutions
Simulating Nuts and Bolts: The Quest for Accurate and Efficient Virtual Prototyping
Accelerating Virtual Simulation: Breaking the 10,000x Speed Barrier
Empowering Robots: Teaching Efficient Object Manipulation through Simulation
Conclusion
Exploring the Challenges of Robot Arms: From Expensive Customization to Unreliable General-Purpose Solutions
Exploring the Challenges of Robot Arms: From Expensive Customization to Unreliable General-Purpose Solutions
Robotic arms have become an integral part of modern manufacturing, helping to build products efficiently and cost-effectively. However, the current solutions present significant challenges. On one hand, the robotic arms used in factories are highly specialized and tailored to specific tasks, making them extremely expensive. On the other hand, general-purpose robot arms are much cheaper, but they are also much more unreliable and slow.
To address these issues, researchers have explored the potential of training robots in simulation, where they can learn to assemble a wide range of objects before applying that knowledge in the real world. However, this approach is not without its own challenges. Simulating the intricate interactions between small components, such as nuts and bolts, requires an extremely fine level of detail, which can lead to computationally intensive and unrealistic simulations.
Fortunately, recent research has proposed innovative solutions to overcome these obstacles. By developing new methods for representing the geometry of complex objects and optimizing the simulation algorithms, researchers have been able to create highly detailed and accurate virtual environments that can run in real-time, even with thousands of interacting components. This breakthrough paves the way for the development of virtual factories that can train robots to perform a wide range of assembly tasks with a high degree of reliability and consistency.
Simulating Nuts and Bolts: The Quest for Accurate and Efficient Virtual Prototyping
Simulating Nuts and Bolts: The Quest for Accurate and Efficient Virtual Prototyping
Simulating the interaction between nuts and bolts in a virtual environment is a challenging task due to the complexity of the geometry and the computational requirements. Traditional approaches, such as using convex decomposition or triangle meshes, have limitations in terms of accuracy and performance.
This paper proposes a novel approach to represent the geometry of nuts and bolts in a way that can provide a highly detailed simulation while running in real-time. The key innovations include:
- A new geometric representation that can capture the intricate details of the nuts and bolts, allowing for accurate collision detection and response.
- A significant reduction in the number of contact points that need to be computed, from 16,000 down to just 300, resulting in a 98% performance improvement.
- The ability to simulate tens of thousands of nut and bolt interactions per second, enabling large-scale virtual prototyping.
- The integration of a resonating feeder mechanism for sorting the nuts, allowing for a seamless simulation of the entire assembly process.
- The development of a reinforcement learning-based approach to teach robots how to properly pick up and screw in the nuts, achieving success rates of up to 85% in the worst-case scenarios.
The combination of these advancements allows for the creation of highly accurate and efficient virtual factories, where the entire assembly process can be simulated and optimized before being implemented in the real world. This breakthrough paves the way for significant advancements in the field of virtual prototyping and robotic automation.
Accelerating Virtual Simulation: Breaking the 10,000x Speed Barrier
Accelerating Virtual Simulation: Breaking the 10,000x Speed Barrier
This paper proposes a novel approach to accelerate virtual simulations, particularly in the context of robotic assembly tasks. The key challenges addressed include the high computational and memory requirements associated with simulating detailed geometries, such as nuts and bolts, and the need for efficient collision detection and response.
The researchers present a multi-pronged solution that significantly improves the performance of virtual simulations. First, they introduce a new representation for detailed geometries that can capture the intricate features of objects like bolts, while maintaining real-time performance for collision detection and response. This breakthrough allows for highly accurate simulations of complex parts.
Furthermore, the paper describes a method to drastically reduce the number of contact points that need to be computed, from 16,000 down to just 300. This 98% reduction in computational load enables the simulation of tens of thousands of nut and bolt interactions per second, a remarkable achievement that brings virtual factories closer to reality.
The researchers also demonstrate the versatility of their approach by simulating a wide range of commonly used parts, including a virtual USB-A adapter, with millimeter-level accuracy. Additionally, they present a technique for teaching robots to properly use these simulated objects, achieving success rates of over 85% in tasks like picking up and screwing in a nut.
The culmination of these innovations is a virtual simulation system that is over 10,000 times faster than previous methods, while maintaining a high degree of realism and accuracy. This breakthrough paves the way for the development of highly efficient and scalable virtual factories, where multiple simulations can run concurrently on a single graphics card, unlocking new possibilities for robotic assembly and manufacturing.
Empowering Robots: Teaching Efficient Object Manipulation through Simulation
Empowering Robots: Teaching Efficient Object Manipulation through Simulation
This research proposes a novel approach to enable robots to efficiently manipulate objects, such as nuts and bolts, through simulation-based training. The key challenges addressed include:
-
Accurate Geometric Representation: The researchers developed a method to represent the detailed geometry of objects like bolts, allowing for highly accurate collision detection and simulation.
-
Efficient Simulation: By reducing the number of contact points required for simulation, the proposed technique achieves a remarkable 98% reduction in computational complexity, enabling the simulation of tens of thousands of nut-and-bolt interactions per second.
-
Transferring Learned Skills to Reality: After just an hour and a half of training in the simulated environment, the robot was able to achieve a success rate of over 85% in picking up and screwing in nuts, outperforming human capabilities in terms of consistency and precision.
The significance of this work lies in its ability to bridge the gap between simulation and real-world object manipulation, empowering robots to tackle complex assembly tasks with unprecedented efficiency and reliability. This breakthrough paves the way for the development of highly capable robotic systems that can be seamlessly integrated into various industrial and manufacturing applications.
Conclusion
Conclusion
The research presented in this work has made significant advancements in the field of robotic simulation and assembly. By addressing the challenges of accurately representing complex geometries, reducing computational requirements, and enabling efficient learning of robotic manipulation tasks, the researchers have paved the way for a new era of virtual factories and automated assembly processes.
The ability to simulate thousands of nut-and-bolt interactions in real-time, with a success rate of up to 85%, is a remarkable achievement that showcases the power of innovative algorithms and computational techniques. This breakthrough not only enables the simulation of large-scale assembly scenarios but also provides a platform for training robots to perform these tasks with a high degree of reliability.
The implications of this research are far-reaching, as it opens up new possibilities for the automation of manufacturing processes, the rapid prototyping of products, and the optimization of assembly workflows. By leveraging the capabilities of virtual environments, researchers and engineers can now explore and refine robotic solutions without the constraints of physical limitations, ultimately leading to more efficient and cost-effective production systems.
The presented work is a testament to the remarkable progress that can be achieved through collaborative research and the relentless pursuit of innovative solutions. As the field of robotic simulation and assembly continues to evolve, the insights and techniques developed in this study will undoubtedly serve as a foundation for further advancements, ultimately transforming the way we approach the challenges of modern manufacturing and automation.
FAQ
FAQ